PROJECT OVERVIEW
The Progress Energy Nuclear Power Plant is located in Southport, NC and consists of two General Electric Boiling Water nuclear reactor generating stations. Due to its unique location near the Cape Fear River and the Atlantic Ocean, the plant draws its cooling water in from the Cape Fear River where it flows approximately 2 miles down a man-made canal. Once the water is used as coolant for the steam turbine condensers, it is discharged from the plant to the Atlantic Ocean via a 5.5-mile man-made canal, passing through a massive tunnel underneath of the Intracoastal Waterway (Figure 1). As seen in this satellite photograph, the plant is massive, and is a significant engineering and construction achievement.
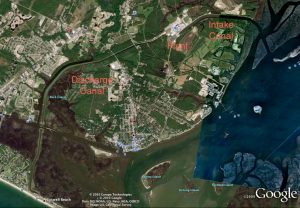
Figure 1. Progress Energy Nuclear Power Plant Coolant Flow Canals
To prevent marine life such as fish and turtles, along with marine sea grass from entering the plant, a large Diversion Structure was built at the inlet of the Intake Canal. This 30-year old structure is V-shaped, with the annex facing the Cape Fear River at the center of the structure (Figure 2).
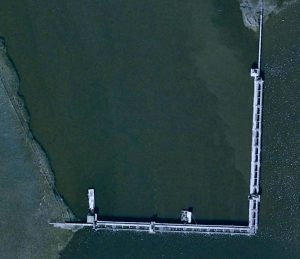
Figure 2. The Diversion Structure
It consists of 2 end pile bents and 13 interior bents. Each bent is made up of four 24-inch square concrete piles with an imbedded H-Pile stinger in the end for driving. The tips of the piles are located at approximately -40 feet mean sea level with pile the stingers protruding an additional 10 feet into the bottom. A wire mesh screen and turtle excluder is maintained between each bent, and can be raised for cleaning by each of two special cleaning rigs on each leg of the structure (Figure 3).
Figure 3. Diversion Screen and Turtle Excluder
The screens rest on a seat beam affixed to the top of sheet pile extending to the bottom approximately 20 feet down from the surface of the water. With both reactor plants online drawing cooling water, and depending on the tidal level, there can be up to 3 feet of differential head on each of the screens. This differential pressure (DP) is felt for the entire vertical length of each screen, resulting in very large forces applied to the structure during high DP conditions. Of note, hurricanes and tropical storms can produce unusually high tides, which further increase the DP imposed on the structure. As a result of recent storms last decade, two of the structure bents have moved inward (away from the Cape Fear River) with a maximum deflection of 9-3/4”. If left uncorrected, this condition would further worsen, forcing the plant to be shutdown pending repairs.
Progress Energy contracted a well-known and reputable engineering firm to design a corrective system of driven piles to shore up the structure and prevent further movement. Taylor Bros. Marine Construction, Inc. (TBM) was contracted by Progress Energy to drive two test piles, and perform the subsequent installation of the driven pile system.
This project showcases that driven piles can be installed in the toughest of marine environments, and are often times the only viable solution to a problem encountered in the marine environment. It further illustrates that pile driving and foundation drilling often go hand in hand when soil conditions dictate, and that project owners and contractors should consider contingency plans for this necessity prior to generating contract documents, rather than after a problem has been encountered. It also illustrates the necessity to perform an adequate number of pre-job borings regardless of the apparent extra costs. The initial impending failure of the structure (movement) illustrates the need to ensure that the driven pile is installed per the minimum driving criteria to achieve success.
Continue Reading (PDF) >>